A Comprehensive Overview to Welding Inspection Techniques and Finest Practices for Quality Control in Fabrication Projects
Welding examination functions as a basic column in making certain the architectural integrity and safety and security of produced projects. Utilizing a variety of strategies-- ranging from aesthetic assessments to advanced approaches like radiographic and ultrasonic testing-- provides critical insights into prospective defects that may undermine stamina. Developing reliable practices and a robust quality management system can boost compliance and integrity. Nonetheless, the details of these strategies and their implementation usually increase pertinent questions regarding the tools and criteria required for optimum end results. What certain techniques will be most efficient in your tasks?
Value of Welding Inspection
Welding examination is an essential part in guaranteeing the integrity and security of bonded structures. The procedure involves a systematic assessment of welds to recognize any kind of issues that may compromise the stamina and longevity of the end product. Efficient assessment is important not only for conformity with sector requirements and regulations but also for safeguarding the wellness and safety and security of employees and the general public.
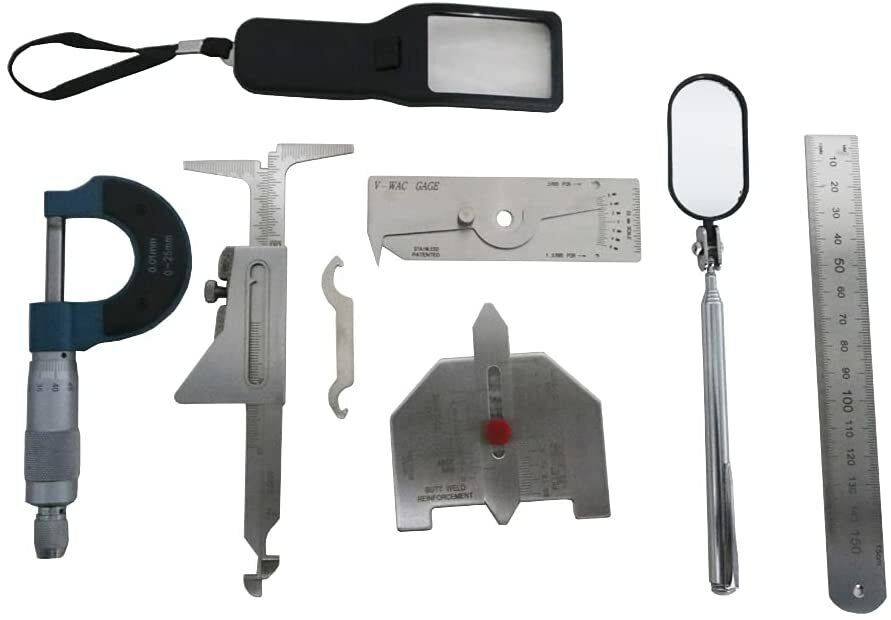
Additionally, welding examination offers as an important device for constant improvement in construction procedures. Inevitably, prioritizing welding evaluation promotes a culture of quality guarantee, ensuring that projects fulfill both client assumptions and regulatory demands.
Usual Welding Examination Techniques
Numerous methods are employed to examine welds, each tailored to find specific kinds of defects and make certain quality. Amongst the most generally used approaches are visual examination, ultrasonic testing, radiographic screening, magnetic particle screening, and color penetrant screening.
Aesthetic examination is the most simple technique, allowing assessors to determine surface area irregularities such as cracks, porosity, and damaging. Ultrasonic testing utilizes high-frequency acoustic waves to detect interior defects, giving a comprehensive assessment of weld stability. Radiographic testing uses X-rays or gamma rays to produce pictures of the weld, exposing inner problems that are not noticeable to the naked eye.
Magnetic particle screening is specifically efficient for ferromagnetic products, recognizing surface area and near-surface problems by applying magnetic areas and using fine particles that indicate abnormalities. Dye penetrant screening entails using a tinted dye to the weld surface area, which leaks into cracks and is disclosed under ultraviolet light, making it easy to detect problems.
Each of these techniques plays an important role in maintaining welding quality, and the choice of an appropriate approach depends on the particular requirements of the construction project, including material type, weld setup, and the wanted degree of assessment.
Crucial Evaluation Devices
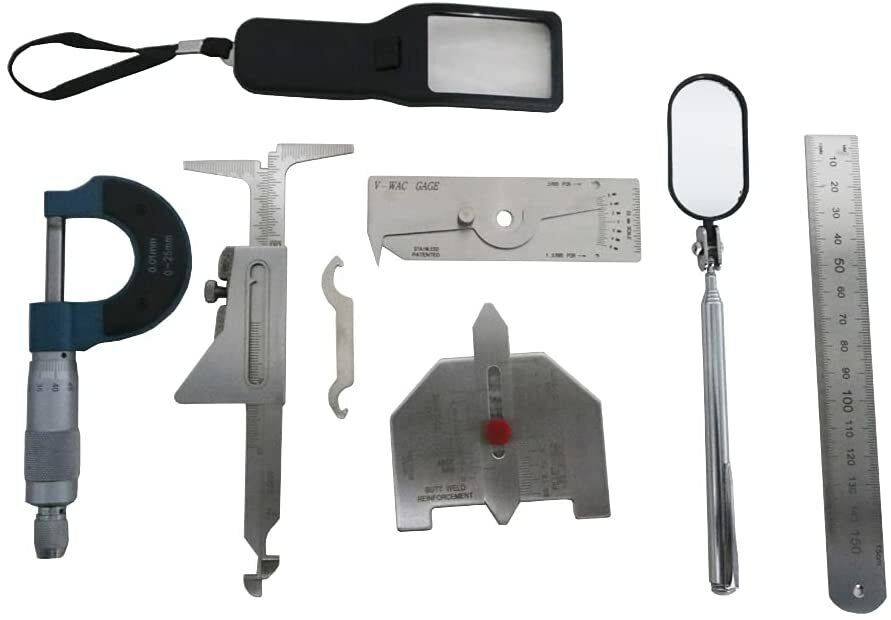
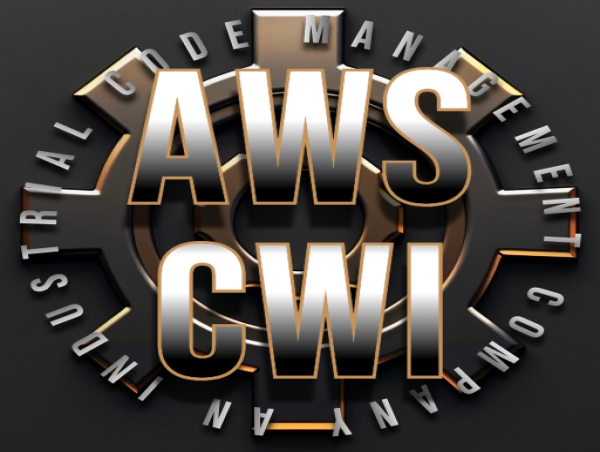
Determining tools, including calipers, gauges, and leaders, are essential for verifying tolerances and dimensions. These instruments aid make certain that welds satisfy the required requirements for strength and resilience. In addition, ultrasonic testing tools are used to detect internal imperfections without endangering the integrity of the weld. This non-destructive screening technique is essential for recognizing issues that may not show up externally.
One more essential tool is the firmness tester, which analyzes the mechanical residential or commercial properties of a weld and identifies its suitability for certain applications. Welding examination software application help in documenting findings, promoting information analysis, and making sure compliance with sector requirements. With each other, these necessary evaluation tools develop a detailed toolbox that supports the welding inspection process, inevitably adding to the top quality guarantee of construction projects.
Ideal Practices for Quality Control
In the search of high quality assurance, carrying out best methods is important for attaining reputable and constant welding end results. Developing an extensive welding top quality management system (WQMS) is fundamental. This system needs to encompass defined procedures, requirements, and paperwork techniques that lead every stage of the welding process.
Routine training and certification of welding personnel are vital. Proficient welders with updated expertise of methods and safety and security measures add considerably a knockout post to top quality. In addition, carrying out pre-welding evaluations makes sure that materials and tools meet specified standards, decreasing the possibility of defects.
Incorporating real-time tracking during the welding process permits immediate discovery of abnormalities, enabling corrective activities to be taken immediately. Post-welding assessments, including aesthetic checks and non-destructive testing (NDT), are crucial in verifying weld stability and compliance with sector standards.
Furthermore, preserving precise documents of assessments, weld criteria, and corrective activities cultivates a culture of liability and constant improvement. Involving stakeholders in regular top quality evaluations can additionally enhance the general performance of quality control measures. By sticking to these ideal practices, organizations can significantly raise their welding quality guarantee efforts, consequently making sure project success and customer fulfillment.
Enhancing Security and Compliance
Attaining high standards in welding high quality assurance normally lines up with the important of enhancing security and conformity within the sector. Efficient more information welding evaluation methods are critical in identifying prospective dangers and guaranteeing that all procedures stick to regulatory standards. These strategies not just offer to keep structural integrity but also safeguard the health and wellness of employees associated with construction tasks.
Applying rigorous examination procedures, such as aesthetic assessments, non-destructive testing (NDT), and thorough documentation, establishes a culture of security and accountability. Training welders and assessors in existing safety laws and best methods is crucial. This makes certain that all employee know prospective threats and are furnished to alleviate them.
In addition, compliance with sector criteria, such as those set by the American Welding Culture (AWS) and the International Organization for Standardization (ISO), is non-negotiable. Normal audits and assessments help determine gaps in security actions and promote constant renovation - Welding Inspection Milwaukee. Eventually, a dedication to boosting safety and security and conformity not only cultivates a more secure working environment but also causes premium quality end he said results and decreased liability for organizations engaged in welding fabrication
Final Thought
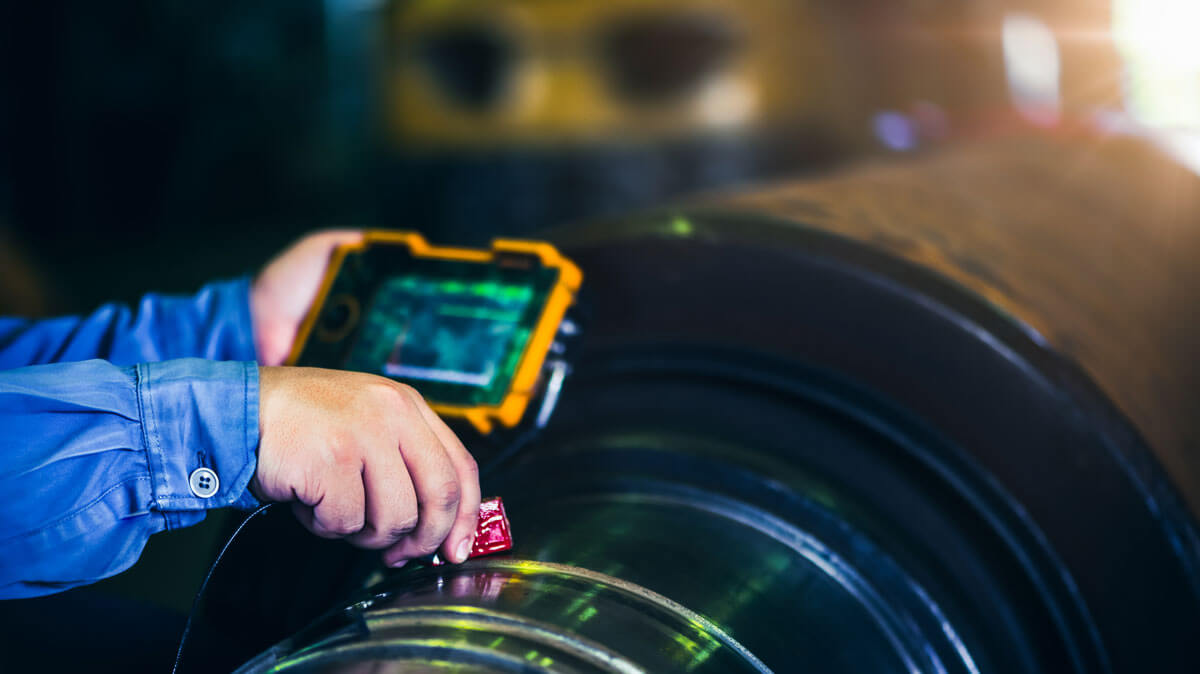
Welding inspection serves as a fundamental column in ensuring the structural integrity and security of produced jobs.Welding examination is an important component in guaranteeing the stability and security of bonded structures. Ultimately, focusing on welding inspection fosters a culture of high quality assurance, making sure that tasks fulfill both consumer expectations and regulatory needs. Together, these important examination tools form a thorough arsenal that supports the welding assessment process, eventually adding to the top quality assurance of manufacture jobs.
In final thought, efficient welding evaluation is important for making certain the architectural integrity and security of fabricated projects. Welding Inspection Milwaukee.